Table of Contents:
- Purpose
- Batteries
- Backup Charger
- Solar (PV) Panels
- Charge Controller
- Circuit Breaker Panel
- Basic Block Diagram of the 12-Volt Solar Power System
- Distribution Wiring
- Modifications to Existing Lamps & Fixtures
- Connectors & Power Outlets
- "You Cannot Manage What You Cannot Measure"
- Future Projects
- Resources & Links
Purpose:
Once upon a time in America, over a hundred years ago, we were well underway toward living Off-Grid.
Pretty much because there was no grid, except in the cities. A multi-million dollar industry was well developed and already in
place producing thousands of products that ran off 36-volt D.C. These homes were powered by
their very own
Delco-Light power plant or a Zenith Wincharger running on their farm or property.
But this entire industry was killed off by the
Rural Electrification Act of 1936 .
[ See: WWW.HybridElectricHome.com ]
Forty years later with the advent of the Solar Panel, we have been slowly crawling our way back to the hayday of generating one's own power, and living comfortably off it. And so the story begins... again...
The purpose of this webpage is to show others how easy it is to install and operate a Solar Power system for your home. Nothing says that you must convert Solar power into 110 volts A.C. (Alternating Current) as most Solar installations do. This is costly and in my view, very inefficient. Every power conversion comes with additional expense, complexity, energy loss, and yet another point of failure. Though modern Inverters have become very efficient, they remain a complex, single point of failure, that I would rather not have to depend upon. So my home power system uses the D.C. (Direct Current) power produced by the Solar panels that has been stored in a battery bank, and then used to directly power LED lights and other devices found throughout the home.
To accomplish this, I have rewired many conventional light fixtures throughout my home to operate with either 110vac or 12vdc, seperately or at the same time. These modifications are easy to implement and don't require you to be an engineer or an electrical wizzard. The most time consuming part of the project was fishing the 12vdc wiring through the attic, walls, and basement to get 12 VDC to each of the lights/devices safely. I strongly recommend taking some time to sit back and think through your specific needs, considering your homes construction before running any wires. A little time spent planning will pay off in the long run if you consider all the issues and you think it through thuroughly. Having experience pulling alarm, telephone, and power cabling in my younger years, I have developed the skills, tools, and techniques to do these jobs efficently. Though at 66 years old they are NOT as easy a task as they were when I was a much more flexible 20 year old!
A benefit to 12VDC Solar Power is that my lights will never go out, even after MONTHS or even YEARS of having no commercial power. Another is that Solar Power offsets a fair chunk of my monthly DTE Energy bill by providing the 12 volts D.C. that is used to run several Ham Radio rigs (both my wife and I are Ham/Amateur Radio Operators), alarm system, and lighting throughout our home. Every little bit helps, and each month or two I add yet another improvement or expansion to the existing system. This is convienient, because I don't have to jump into a Solar power system all at once, nor lay out a bunch of cash or take on a huge wiring project all at once. This lets my "learning curve" evolve a little at a time, thereby avoiding what could perhaps turn in to some rather expensive mistakes. Take your time and plan ahead.
With regard to migrating off commercial power and onto solar a little bit at a time - I happen to watch a fair amount of TV. While we tossed the big old energy hungry CRT TV sets awhile ago, the newer flat screen TVs are far more efficient. As it happens, they are typically powered by a "brick" power supply much like those used for laptop computers. My flat panel TV requires 19-volts DC and consumes up to 60 watts. So I aquired from Amazon a couple DC-to-DC converters that allow me *step up* the 12 volts to 19 volts to run the TV set. By getting this 60 watt load that is powered ON for many hours every day moved onto FREE Solar power, should result in a marked decrease in my monthly power bill!!!
So the overall theme here is, DO SOMETHING, DO ANYTHING! Just do little baby steps toward gaining your independance from the commercial power lines. Every step forward is a step in the right direction!
Batteries:
We will start with the heart of the system, and that is the Battery Bank. This is where we draw power from to run all of our lights, radios, TV, Laptop, and other devices, known as "loads". The batteries are the core component of our power system. All loads run off of the batteries, while all the power we generate for free from the solar panels, is pumped into the batteries to keep them charged.
The Battery Bank MUST be able to provide ALL of our power needs throughout the night and on those bad weather days when the Sun is not shining due to rain, snow, or simply cloudy and overcast. The suggested goal is to have enough Battery Capacity to run ALL your needs for at least THREE DAYS without requiring a recharge. That can sometimes be a real feat to accomplish! I currently have enough battery capacity for THREE to FOUR days, but that was accomplished by adding battery capacity as I could afford to. It does not all have to be done at once. As more LOADS were added, I also added more battery capacity to match. But start SOMEWHERE! Your system will grow over time and so will your battery needs and capacity.
But what type of battery should you buy? That may depend upon your budget and your specific
requirements. There are several battery chemistries you can choose from. The most well known
is the Wetted Lead-Acid battery. This battery uses two lead-based plates seperated by a thin
pourous membrane and uses Sulfuric Acid as the electrolyte. These batteries are large, and heavy, but
are relatively inexpensive per Amp-Hour and are easy to maintain. Wetted Lead-Acid batteries can be
charged and discharged rather rapidly, which makes them excellent for heavy loads. They are what is
used to start your car. A much beefier form of this battery is called a Deep Cycle battery
because it can withstand thousands of deep discharge cycles, which your flimsy car battery cannot.
Deep Cycle batteries are used in Golf Carts, Fork Lifts, and large Uninteruptable Power Supplies (UPS),
because of their low cost per Amp-Hour of capacity and long life cycle. Hence, these are an excellent
choice for our Solar Power applications.
[ Wetted Lead-Acid Deep Cycle -- $170 for 210 Amp-Hours at 12-volts ]
A very similar battery is the Sealed-Lead-Acid (SLA). This is similar to the Wetted Lead-Acid
except that it uses a paste as the electrolyte. The paste makes it very hard to spill, but it also
limits the rate that the chemical reaction can occur, thus limiting the rate at which they can be
charged or discharged. These batteries are excellent for environments where spillage is of concern,
and do not have to be upright since the electrolyte cannot leak out. The downside is that they cannot
be charged at high rates because the heat produced can cause bubbles in the electrolye paste eventually
causing pressure to build forcing the emergency release vent to open. If you hear your battery hiss,
it's life is basically over. So charge and discharge rates need to be tightly controlled.
[ Sealed Lead-Acid (SLA) -- $30 for 7 Amp-Hours at 12-volts ]
A more recent newcomer to the battery market is the Lithium Iron Phosphate (LiFePO4) battery, also
called LFP battery (with "LFP" standing for "lithium ferrophosphate"). These batteries have a very
high "Energy Density" and are light weight for their Amp-Hour capacity. They can be charged and
discharged at a rapid rate. You will want your battery to have a built-in "BMS" Battery Management System. The BMS assures that the battery does not over heat nor is charged below 40 degrees, as this will cause permanant damage to the cells. The BMS also manages the voltage of each cell so they all perform equally and that helps to extend their life.
These batteries can be charged and discharged many THOUSANDS of times if you keep the charge/discharge between 20%/80%. And for voltage sensative loads, the LFP will maintain a 13.6 volt "terminal voltage" through 80% or more of its discharge cycle, permitting you to extract energy well into the discharge cycle before you see a voltage drop.
At $300 for a 100 A/H battery they provide a great bang-for-the-buck. An added benefit is that LiFePO4 does not have the "thermal runnaway" problem that Lithium-Ion does, so it is not likely to be a fire hazard.
These batteries weigh in at 1/3rd the weight of Lead-Acid, at about 22 pounds for a 100 A/H battery.
[ Lithium Iron Phosphate -- $300 for 100 Amp-Hours at 12-volts ]
A very old battery chemistry is the Nickle-Iron "Edison" battery. These batteries use elecrodes
made of Nickle and of Iron, and use an electrolyte consisting of Potassium Hydroxide. They produce
a lower voltage per Cell (around 1.2 Volts), so more cells are required to make a battery of a particular
terminal voltage - 10 cells for a 12-volt battery. But these batteries can withstand enormous
amounts of abuse when charging and discharging! And they are known to last for well over 100 YEARS!
About the only way to kill one is to let the electrolyte dry up, hence Edison suggested putting
a layer of Mineral Oil on top of the electrolyte so that it cannot evaporate. Some DIY Preppers
have been known to build Cells out of 55-gallon drums and have reported 5000 Amp-Hour capacities
for only about $100 per cell. That's 5000 Amp-Hours that can be used for longer than you will be
alive, and costs about $1000 to build. Something to leave your grandkids. However, commercially
available Ni-Fe batteries cost a bit more.
[ Nickle-Iron "Edison" -- $970 for 100 Amp-Hours at 12-volts ]
My battery bank used to use Wetted Lead-Acid type battery because it is inexpensive for the amount of Amp-Hour capacity it can hold. I have ample room to house the batteries so size is not an issue, and weight is not an issue at all. With good care, Wetted Lead-Acid Deep Cycle should provide near 10 years of dependable service before needing replacement. I have since migrated to LiFePO4 as they are SAFER, maintenance free, and provide MUCH better terminal voltage charactoristics over a wider discharge cycle.
Back in the 1970's I began powering my Ham Radio equipment using old car batteries, I later replaced
them with 55 Amp/Hour wheelchair batteries. These were better as they were meant to be discharged
daily, while car batteries are not. Then as my needs continued to grow I replaced those with 6-volt
Golf Cart batteries as they have MUCH more capacity (Amp/Hour Rating) and are designed for daily deep
cycle use. Costco sells such Golf Cart batteries for $85 each ($100 if you don't turn in a dead battery
as a "core"). A pair of 6-volt Golf Cart batteries provides me with a dependable deep-cycle supply
of 210 Amp-Hours (for each 12-volt string).
[ Golf Cart Lead-Acid -- $170 for 210 Amp-Hours at 12-volts ]
In this photo (this is not my battery bank, but a nice example) you can see where three 12-volt strings of batteries have been placed in PARALLEL to combine their respective Amp/Hour rating into a much larger capacity bank. Let's say that each 6-volt Deep Cycle battery has an AmpHour rating of 210 AH. Two 6-volt batteries in SERIES gives us 12-volts, but the AH capacity of the string is still 210 AH. By putting three strings in parallel (assuming all the batteries are of the same capacity) we still have 12-volts but we now have an Amp/Hour capacity of 630 AH.
I *highly* recommend keeping battery cables tight and clean, and all cables should be of the
largest wire gauge practicle. This assures the lowest losses. Smaller gauge wire will act
like a resistor as large currents run through it. It is also better to extract the POSITIVE
lead from one end of the bank (large RED cable in the top left of the photo) and the NEGATIVE
lead from the opposite end (large WHITE wire in the lower right of the picture).
This is to cause the current flow through each battery AND CABLE to be equal as much as possible. Some
battery banks even cross-connect between each of the 6-volt batteries to reduce any imballances
in the bank.
Batteries in SERIES need to be of the SAME capacity so that all cells charge equally. Batteries in PARELLEL may be of different capacities because it is only their Terminal Voltage across the string that will matter as they will charge or discharge equally, together as a group.
Since all batteries have a bare minimum Terminal Voltage that you should NEVER discharge below, we will need to assure that the Battery Bank never discharges below that point. The rule is to NEVER let a 12-volt string discharge below 11-volts or permanant damage WILL occur! So we will keep the batteries charged using two methods. First, the FREE method, and that is to use an array of Solar Panels combined with a Solar Charge Controller which will keep the battery bank topped off at between 13.5 and 14.4 volts. This keeps everything running and provides a charge (or re-charge) to the batteries whenever we have sunlight. More on that, later.
But sometimes you just won't get enough Sun to make ends meet (bad weather, shorter Winter days, etc.). So at these times we need some kind of backup system. Enter the Backup Charger. This is nothing more than a regulated power supply that keeps the batteries charged to a specific terminal voltage. A voltage of 13.2 is a "float" charge level that keeps the batteries fully charged while not causing any off gassing. Fully charged batteries under load *should* hover around 12.6 volts. But once they start to drop below this voltage, they have begun to discharge. So we like the backup charger to maintain a voltage somewhere between 13.2 and 13.6 volts to keep the batteries fully charged while not off-gassing. I typically don't turn on the backup charger unless we are not getting enough charge off the Solar panels.
Backup Charger:
In my basement office and combined Ham Radio Shack, are my battery bank and much of my Ham Radio equipment. The batteries are close to the Ham Radio equipment because they are the largest LOAD, that are placed on the batteries. While transmitting I will typically draw anywhere between 5 and 20 Amps. So cabling is kept as short as possible to reduce what are called "IR Losses" (the voltage dropped across the resistance of the wire). More on that later.
For the same reason, the Charger is kept close to the battery bank. The Charger is a simple
IOTA DLS-55 55-Amp 13.6 volt power supply.
This supply is able to keep the battery bank State of Charge topped off sufficiently
while a number of LOADS are turned on or in use.
The backup charger is *rarely* ever turned on, except for the months of December/January/Februrary when we have very heavy overcast skies here in Michigan. For most of the year the Solar chargers will meet the needs of the loads and keep the battery bank fully charged.
Remember to try to size your battery bank to support ALL
your needs for THREE DAYS, preventing the Terminal Voltage from dropping to where you will need
to recharge them. Then if you still don't have a clear weather day, you can always resort to turning
on the Backup Charger to return the batteries to a safe State Of Charge before any damage is done.
An advantage of the IOTA DLS-55 power supply is that it puts out 13.6 volts at up to 55 Amps.
By added the (included) profile jumper, that voltage goes up to 14.4 volts which is perfect for charging Lithium-Iron-Phosphate (LiFePO4) batteries.
But it gets even better if you add the IOTA "IQ4" Charging Module.
This $20 module converts the DLS-55 into a "two-stage" Constant-Current / Constant-Voltage charger. It will RAPID charge your LiFePO4 batteries at 50+ Amps constant-current until the batteries are near capacity, then switch to the the Constant-Voltage mode to maintain the batteroes at 13.6 volts. And periodically (about every two weeks) it will automatically go to Constant-Current mode to top off the batteries.
An additional advantage of the 2-stage CC/CV charging is if you have a heavy snowstorm and the Grid goes down. Your PV panels are covered in snow and not producing, and you have no Grid power to fall back on. By rapid charging the batteries while running off of a gasoline generator will reduce the number of hours you need to run the generator, reducing your fuel consumption.
Solar (PV) Panels:
The primary source of power comes from an array of solar panels, also known as "PV" or
Photo Voltaic cells. I started with the PVL-128
flexible (Amorphouse) panels rather than the typical glass/fixed panels. Each strip had
22 cells and can produce up to a maximum of 128 watts. They are 19-feet long and 16-inches
wide and have an adhesive backing as they were intended to be installed in the troughs of metal roofing.
These are not the most efficient per square foot, but the price was right - and I have plenty
of roof space to fill.
The PVL-128 has an "Open Circuit" voltage of 33 volts. This is the voltage the panel will
output under no load. When matching a Charge Controller with your panels you MUST not
excede the maximum input voltage for the charger!
So PLAN your installation accordingly.
There are many varieties of PV panels available. As you will see in this chart they all have basically the same power prudction performance (per square meter). This is the number of Watts produced on a perfectly clear day ON THE EQUATOR. Unless you live on the Equator, you will never get the total output power listed on the panel. All PV panels are rated against this same parameter. The typical energy efficiency is around 19% no matter what panel you buy.
There are many other factors that affect the output, such as the angle the panel is toward the Sun. For best performance this should be perpendicular to the Sun. But don't worry too much about needing a "tracking system', as panels these days are manufactured with fine metal strands in the glass that reflect the Suns rays downward toward the PV elements. The Sun can be off-center by 45 degrees or so, and you will still extract full power.
Since most people mount their PV panels flat onto their roofs, they never actually point toward the Sun. For best performance they should be mounted at an angle equivelant to your Latitude. Here is Southeastern Michigan I should tilt my panels at roughly 43 degrees. However, mine are mounted on a 4:12 pitched roof, that's about 18 degrees - so I accept a little additional loss for asthetics. Some ground-mount systems will mechanically tilt their arrays a couple times per year as the Sun is LOW in the sky during the Winter, and HIGH in the sky during the Summer. This difference is typically around 23 degrees.
Those of you who are North of 45 degrees Latitude, it is MORE efficient to mount your PV panels VERICALLY on the side wall of a garage or pole barn. And as an added benefit, the snow will never collect on your panels!
EFFICIENCY PER SQUARE METER The amount of energy striking the Earth at the Equator is roughly 1000 Watts per square meter. The efficiency of the highest quality PV panel is only
about 20% at best. Many PV panel manufacturers will advertise significantly higher output power than their competition. This is only achieved
by making their panels LARGER is surface area, as the efficiency is still only around 19%. Unless there is a breakthrough is PV technology,
this limit will be with us for a while. There are many manufacturers working on improved technologies that are very promising.
Pictured here are 14 of my 16 PV panels used for my "Grid Tied" system. This system is rated at 5.12 KW, but due to my Latitude and the angle to the Sun, will more practically produce 3.85 KW of power on a clear Summer day. It is Grid-Tied but my Inverters are set to NO EXPORT so no energy is sent out onto the Grid as I have no contract with my power company.
Modern day solar panels cost in the vicinity of 50 cents to $1 per Watt. So my PVL-128 panels *should* have cost me anywhere between $65 to $128 at todays Price-per-Watt pricing. A 250-Watt glass panel used to sell for $300 each, but now sell for much less than this, depending upon manufacturer and provider.
You must understand that *efficiency* per square foot is ONLY important if you have very limited square footage to install panels on. I have an abundance of South-facing roof on both my garage and my home, and I can place "racks" in my side yard, if necessary. So efficiency per square foot wasn't my concern, but money out of pocket to get this project started, was!
I'll note here, that many people hold off purchasing solar equipment because the price continues
to drop and the efficiency continues to go up. This is called "Annalysis Paralysis", where you
NEVER get a solar system installed because you are constantly waiting for the next improvement
in the technology or drop in price. So you totally miss the bus!!! Do SOMETHING! And do it NOW!!!
Like any technology, in the future you can always buy something newer or better. Buy it NOW, then
when you are ready to jump to a better technology, SELL your older stuff to the next guy, a friend,
or a neighbor, who wants to get started but can't afford the latest and the greatest.
IronRidge Racking System:
URL
FF2
XR-100 extruded aluminum slotted rails
UFO Universal Fastener Object
End Caps
Total flexibility in positioning, up/down left/right.
Online Design Tool
BOM which can be sent to your local vendor to fulfill your order
Spec sheets for the Permiting process with your local building department
Solar Shed:
As a Summer project I constructed a 6 foot by 22 foot Solar Shed. The dimensions
were selected based on many factors - it had to hold certain powered yard tools such as a
Troy-Built "Horse" Rototiller, electric lawn mower, fertilizer speader, etc.
And its sloped roof had to be near
45 degrees (ended up being 35 degrees) and have a large enough surface area to support 12
PV panels. It also could not be taller than the typical 4x8
sheet of T1-11. The shed ended up having two large 5-foot wide barn doors on the front, plus
a 5-foot wide door that folds down to form a ramp to drive the Try-Built Horse in and out,
easily.
The Solar Shed has a metal roof for simplicity, lower cost, and lowest maintenance costs.
This required a slightly different form of IronRidge mounting than is usual. The IronRidge
"Lynx" clamps worked perfectly on the the "raised ridge" metal roofing.
IronRidge makes a special clamp that attaches to the "raised ridge" type of metal roofing
called the "Lynx".
Pictured here is a similar clamp made by "S-5!". S-5! makes many metal roof clamps for dozens of
different roof styles.
For those of you who have a shingle roof, IronRidge also makes the FlashFoot2 that slips underneath a row of shingles
and is fastened to the roof
using a long lag bolt into the roof rafter. A cone is then twisted atop the bolt, providing a mount point for
IronRidge XL-100 rails in either a vertical or horizontal orientation. This provides a VERY watertight mounting
system.
Solar Charge Controller:
Every solar system should have a trustworthy way to take the energy from the solar panels and apply it to the battery bank with the expectation that the batteries will receive their maximum allowable charge without concern of them becoming overcharged or damaged. The purpose of the Solar Charge Controller is to manage the voltage and current from the panels, and apply it to the batteries in the most efficient manner to maintain the proper terminal voltage (13.5-14.4) while not exceeding the proper rate of charge (current). You've got a lot invested in the batteries and you don't want to damage them or shorten their life - nor damage any of your devices attached to the batteries.
Let's examine a couple methods used to accomplish this.
Some charge controllers simply pulse the FULL VOLTAGE output of the solar panels into the batteries at a duty cycle that will produce an Average Voltage of approximate 12 volts. This is called PWM (Pulse Width Modulation). The batteries will absorb these pulses of high voltage because they act much like a giant capacitor. PWM is rather inefficient since the pulse is TURNED OFF much of the time, and during that time you are NOT getting ANY energy from the Sun. PWM is considered only about 50% efficient. But wait! There IS a better way!
Enter MPPT (Maximum Power Point Tracking). Without going into all the "magic" that MPPT does internally, let's just say that MPPT controllers don't do the high voltage spikes like PWM does, but uses a DC-to-DC Switching Regulator instead, and typically are 98% (or more) efficient. They get nearly ALL the energy produced by your PV panels into your battery and/or loads.
See the Microchip AN1521 Application Note for specific details regarding how MPPT works.
The Solar Charge Controller I use is the "Apollo" MPPT Solar Charge Controller made by DIY Solar For U [www.DIYSolarForU.com] located in Troy, Michigan.
The Apollo Solar Charge Controller can accept up to 50 VDC from the PV panels at up to 255 Watts
maximum. Using MPPT technology, it can output up to 16 Amps, or roughly 230 Watts, output
power to the battery and loads. It is roughly 98% efficient so hardly any heat is wasted.
A mighty fine little workhorse for only $125.
Multiple "Apollo" units can be attached in parellel (on the Battery side of the controller) to
allow a larger array of solar panels to charge and maintain one battery bank. So if you need
more than 230 Watts of solar production, just add more panels and controllers. Thus far, my needs
have not exceeded what this controller can provide. Someday I expect I will need more, but the
Apollo is one of the least expensive MPPT controllers on the market. And the company owner is
a Ham Radio operator, so he's alert to making certain that his design does NOT interfere with any
of the Ham radio bands. That to me is an added bonus!
My wife and I are both Ham Radio Operators and we noticed a problem with the charge controller
after using the 100-watt HF radio. Long story short, RF energy from our dipole got into the PV
panel input of the Apollo and caused an FET to go bad. Rob at DIYsolarForU identified the problem
and repaired the controller for free with an improved and less sensitive part. He also updated
the firmware to the latest version. With the addition of a simple RF Choke, my transmitter no
longer has any effect on the charge controller. Rob now sells RF Chokes on his website for all
of $5. I recommend adding the choke in between your PV panels and the Apollo controller if you
are a Ham and expect RF may be an issue.
Another function of the Charge Controller is to perform three, and sometimes four, different
types of charging. These are Bulk, Absorption, and Float. Some chargers also do
Equalization.
Bulk is where the battery is discharged and needs to be recharged as rapidly as possible.
Absorption is where we continue to charge the battery, but at a slower rate.
Float is where the battery has reached its full state of charge and can
now be floated at a voltage sufficient to run all of our loads but low enough that the battery will
not off-gas and lose electrolyte.
Equalization is a process performed once a month that raises the terminal
voltage to an even higher value than normal, in an attempt to bring up any lagging cells. This can
oftentime help an aging string of cells/batteries, but will cost some electrolyte if done too often.
This feature is not available in all Solar Charge Controllers and many users don't find it usefull.
The CapnFatz website is one of the best I have found that covers the internal chemistry
of what is going on inside a wetted lead-acid cell, from discharged to fully charged. This is an
excellent Primer to wrap your head around the charging process. It even delves into
Internal Resistance and Series Opposing resistance.
(click on the image to go to the CapnFatz website)
Circuit Breaker Panel:
So we have our batteries. And we have our backup charger. And we have our PV panels and a way to take that energy and put it into the batteries through a charge controller. Now we need to distribute that energy to the loads - the lights, the fans, the motors, the TV, or anything else we may want to run. But we need to do it SAFELY! We want wiring that doesn't burn the house down and we want some way to turn off circuits when we need to service them. And most importantly, we want a device that will turn off an over-loaded circuit automatically when something has gone wrong. You can use fuses, but I use DC Circuit Breakers to appomplish this task.
Most circuit breakers are intended for AC use. When they disconnect, arcing across the contacts is stopped because with Alternating Current the voltage drops to zero every 8.3 milliseconds. So any arc across the contacts is extinguished very quickly.
But with Direct Current, that arc inside the breaker *can* quickly damage the internal contacts, and can sometimes arc weld themselves together causing the breaker to NOT break the current path! So breakers designed for DC have special mechanical designs that quench the arc mechanically by sliding a non-conductive shield between the contacts as the current path is opened. More complex methods of arc supression exist, but are beyond the scope of this website.
Here we see a 19-inch rack mount panel containing several DC circuit breakers. Each circuit
within the house has a circuit breaker for the protection of the wiring. We want the breaker
to open up the circuit BEFORE the current being drawn is greater than what the gauge of the wire
can carry. Too much current for a particular gauge wire can cause the wire to heat up or melt.
THAT would be a fire hazzard and we don't want that! So, for a smaller diameter wire we use a
circuit breaker rated for a lower current (Amperage).
A larger diameter wire can carry a larger amount of current, so a larger circuit breaker is used.
There are many charts available online that tell what the maximum current capability is for any
particular gauge of wire. I suggest you become familiar with these ratings and abide by them.
You should never mix thin gauge wires with heavy gauge wires on the same breaker, unless the breaker is rated for the for the THIN wire. It is entirely practical to use heavier gauge wires to reduce the voltage drop across a long run. So a large wire might very well be used for low current loads.
Starting from the far right, the circuit breakers are as follows:
10-Amp --- PV Panel Input to the Charge Controller (2 PV panels @4A each)
25-Amp --- Charge Controller Output
100-Amp -- Main Solar Battery Bank (210 AmpHours)
12-Amp --- Battery Bank Tie (between the Solar batteries and the Ham Shack batteries - 150 AmpHours)
12-Amp --- (not currently in use)
10-Amp --- (not currently in use)
10-Amp --- Bathroom Light & (future Laundry room light)
10-Amp --- Kitchen Sputnik Lamp & Hallway Light
5-Amp ---- Kitchen Under-Cabinet strip of LEDs w/dimmer
Basic Block Diagram of the 12-Volt Solar Power System:
....still drawing up a picture that is worth a thousand words...
...in the meantime, this will have to do...
Distribution Wiring:
Obviously, wiring of low-voltage DC circuits is not harmful to life and limb as a shock hazard. But be assured that the DC currents involved *can* cause excessive heat, resulting in the melting of wires and insulation! The potential current available from a large battery bank can be HUGE and the effects can be dramatic and quick, should a short occur. So we MUST take precautions to prevent and protect our wiring from scorthing our household belongings, rugs, furniture, or from burning the house down!!! By selecting the correct Gauge wire for the expected load and by fusing it (breaker) properly, will keep us from having a bad experience, or worse.
To deliver an equivalent amount of POWER over a 12 VDC circuit requires TEN TIMES as much current as it does over a 120 VAC circuit. And to deliver ten times as much current requires a MUCH thicker (larger Gauge) wire. Thankfully, many of our 12 VDC devices are efficient and don't draw much current, so the Power can oftentimes be rather low. But some devices will need HIGH amounts of current, and will need MUCH heavier wire and preferably shorter cable runs to be practical.
The rule to keep in mind is the "IR" rule. Don't confuse this with the I2R rule, we are working with Direct Current here so there are no phase angles involved in the calculation. Simple IR losses need to be taken into account when designing our wiring distribution plan. Current (I) times the Resistance (R) of the length of wire being used, determines our Voltage Drop. And we like to have as little Voltage Drop as possible. While LED lights may not be terribly sensitive to a slight drop in voltage, a fan or refridgerator will be. So understand these losses and design a wiring distribution plan that accounts for them. To make our lives a bit easier, also try to place HEAVY loads nearest to our battery bank as possible and use the heaviest Gauge cable for these runs.
As an example, let's say that we have a 100-foot run of wire that has 0.5 Ohms of resistance, keeping in mind that we need to account for both the path out to the device AND the path back from the device, or 200 linear feet. If we were to put a 3-Amp load on the end of that cable, and the cable presents a 0.5 ohm resistance, we would suffer a 1.5 Volt Drop across the 100 foot cable pair. If we had 13 volts at the battery bank, that only leaves us with 11.5 volts at the device we are trying to power! All due to only a 1/2 Ohm of resistance.
The math goes something like this:
3 Amps times 0.5 Ohms equals 1.5 Volts dropped across that resistance
But if we were to use a much larger gauge wire that has HALF as much resistance (0.25 Ohms rather than 0.5 Ohms) then we can reduce the voltage drop to only 0.75 volts, thus delivering 12.25 volts to the device. The larger the gauge of the wire, the lower its resistance per foot.
As you can see, the IR loses can become significant in low-voltage systems. So pay very close attention to the gauge of wire/cables used, and pay attention to tight low-loss connections, as these will add resistance to the cable loop. Our goal is to have minimal voltage drop. Each loss adds up and will effect the performance of your power system. We want our fans to run strong and our lights to be bright, so it is best to have as much of the 12 to 14 volts delivered to our end device as possible without IR losses.
The charts below will help you determine what gauge wire to use for the desired load current. Keep in mind that these numbers are based on Copper wire. Aluminum or other metals conduct electricity differently, and have different resistances-per-foot for a particular Gauge. If you are using something other than copper, be sure to look up the correct tables for your needs.
Modifications to Existing Lamps & Fixtures:
There are all sorts of 12vdc LED lights available. My preferance has been those that give off as near to natural white light as possible. Many 110 volt CFL screw in bulb replacements have a yellowish tint to them, making reading under such light uncomfortable. The 110 volt LED screw in replacements are much better, and give off a more natural light, but we want to avoid needing 110 volts AC altogether.
My prefered 12-volt LED is the type 5050. This LED has a Color Temperature close
to natural white light, almost as good as the Sun shining into a room on a clear day. Lucky for
us these 5050 LEDs come available on a small panel containing 48 LEDs. This panel has an adhesive
back, making them very easy to attach almost anywhere. They draw approximatly 7-1/2 Watts
per panel, and Amazon sells them for about $8 per pair.
Available on Amazon for $8 is the "Zone Tech Xenon White High Power 48-SMD 5050 LED Panel Light For Car Interior Map/Dome/Courtesy Door/Foot Area/Trunk Cargo Light"
There is a smaller version of the 5050 panel containing only 12 LEDs that also sell on Amazon
for about $12 for a pack of 6. These are excellent for Night Lights in stairwells, hallways,
closets, pantrys, or anywhere you need enough light to see well enough not to trip over something.
Available on Amazon for about $12 is the "EverBright 6-Pack Super White 240lums 3th Generation Energy-saving 5050 12-SMD LED Panel Dome Light Auto Car Interior Reading Plate Lamp Roof Ceiling Interior Bulb With T10 / BA9S / Festoon Adapters (DC-12V)"
Most everyone has seen LED Strip Lights, as these decorate so many stores, bars, and public areas these days. They come in many varieties from just white to colors to colors like a rainbow that change randomly. You can get them in weatherproof as well as non-weatherproof varieties, and they have an adhesive backing so they can be stuck nearly anywhere. I use these under my kitchen cabinets to light my counter top. By using a small $3 PWM brightness controller I can adjust the brightness to just the right amount of light! These too, are available through Amazom and typically are about $1 per foot.
Available on Amazon for about $9 is the "LE 16.4ft 300 SMD 5050 LEDs Flexible Strip Lights, Daylight White, Non-waterproof, 12 Volt"
Available on Amazon for $6 (I got mine for only $3) is the "Leegoal LEDwholesalers LED Strip Lights PWM Dimming Controller For LED Lights or Ribbon, 12 Volt 8/10 Amp, 3301"
UNDER CABINET LIGHTING IN THE KITCHEN:
Under-Cabinet lighting is the big thing these days, and we can all see why. Being able to better see what we are doing on the counter where all the work is being performed is monumental. Lighting those items we keep under the cabinets means that we can easily read the lables on canisters - no more will you pour salt into a recipe when you wanted to add sugar. Cabinets and countertops also look cleaner and better organized when they are well lit. They are also easier to clean when you can see what you are doing.
My under-cabinet lights are left on 24-hours per day, though they are sometimes dimmed at night. Rarely do I have to turn on a light when fetching a snack from the fridge and a plate or bowl to put it on.
This was an easy install. Two rolls of 16-foot type 5050 LED light strips were purchased
via Amazon. Type 5050 LEDs as I explained earlier, are very close to natural white light.
The strips run directly off 12 volts and despite the number of LEDs, are quite low in power
consumpsion. I added a PWM Dimmer to control their brightness, dim at night like a night-lite,
and bright when working in the kitchen. I'll cover the PWM Dimmer in more detail in a moment.
The LED strips are adhesive backed, so CLEAN the surfaces they are to mount to very well.
Nothing sticks well to old kitchen greese. I not only cleaned, but I applied a fresh coat of
paint - hey, I was redoing the cabinets anyway. PLAN the job carefully.
Pre-drill all the holes in the bottoms of the cabinets and
inside shelves so you won't have any dust getting into the adhesive. Apply about a foot at a time
being carefull to get them straight the first time. Working upside down CAN be tedious, so
take your time. And trust me, they don't peel off easily if you have to make any corrections.
There are solder tabs at the ends of the strips, so joining the two strips was easy. I lucked
out that the joint was inside the last cabinet, so my joint is well hidden. There are CUT points
printed on the strips. You can safely cut the strip to length when you have reached the end of
your cabinet. Do this with the power OFF!
The PWM Dimmer is located where the 12 VDC power feeds the LED strip. It is a small box
with screw terminal connections for 12v input and Load output. I located the Dimmer up
underneath the cabinet in a convienient location. The knob is easy to reach, yet out of the way.
Again, an inexpensive buy off Amazon for only $3.
Running the LED strip under the cabinet is one thing, but I was perplexed with how I was going to
continue the strip over the Kitchen sink behind the Valence? I didn't want to have any more
connections that could possibly fail, than necessary. Then it struck me. Rather than cut the LED
strip, I found it was much more easy to route the strip through the cabinets. This offered a feature
that I have since found to be quite handy. I no longer reach inside of a dark cabinet to grab a cup
or bowl or plate. The interior of the cabinets on either side of the sink are well lit inside!
Again, keeping it simple has resulted in a feature that makes life living independant of the grid so
much nicer.
Light over the sink is just as handy as having it on the countertops. So the LED strips are
run directly behind the scalloped valence, offering just enough light to perform simple sink
duties without having to turn on any brighter, more costly lights. The 110-volt fluorescent
gets turned on when the heavy duty work is being done in the sink. Maybe someday even that
light will be replaced with a more efficient high-intensity LED.
HALLWAY LIGHTING:
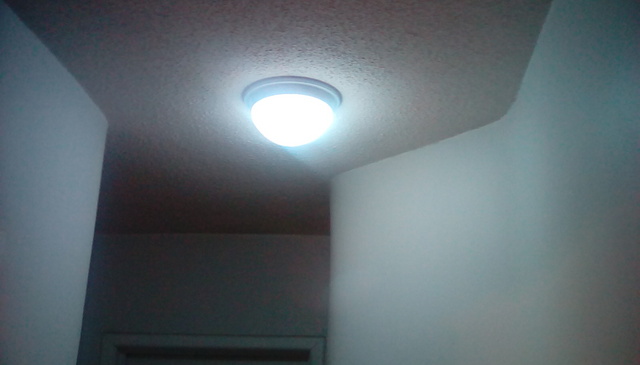
It started with an inexpensive $12 light fixture from Home Depot. The 110vac bulb socket was
removed which left a lot of flat metal surface to attach a pair of 48-LED type 5050 flat panels.
These panels have an adhesive backing so they were VERY easy to attach. Each panel uses roughly
7-1/2 Watts at 12vdc, so two panels gave off a LOT of natural white light (produced by the
type 5050 LEDs) for only 15 Watts of power input.
The 48-LED 5050 Panels were aquired through Amazon for only about $6 per pair. These come with
an assortment of light socket adaptors. I snipped the connector off a couple of these and used
the pre-wired connector to make an easy connection to my 22-gauge wiring, putting the two
panels in parellel.
The 22-gauge was then routed in the attic and down the wall to a standard
"paddle" type light switch. At these low currents, the contacts in the switch should last
for many tens of thousands of operations.
LIVINGROOM LAMPS:
With just a little work in the shop, it was easy to manufacture a simple addition that mounts onto the Halo of almost any typical table lamp. Just two lengths of 1/2x1/2x1/8 inch angle aluminum, a pair of bolts, nuts, washers, and this aluminum frame easily clamps onto the Halo with enough room to leave the 110-volt bulb (preferably a low-heat LED) in the original socket.
Two 48-LED flat-panels are stuck onto each of the aluminum bars. It's convienient that
these light panels come with an adhesive backing - just peal and stick! One panel is
facing upward and one facing downward. These are controlled with a 4-position rotary
switch, the type used in older 3-way lamp fixtures. One click turns on the bottom light
panel, the next click turns on the upper light panel, another click turns them BOTH on, and
the last click turns everything off. Rinse and repeat!
Light can now be directed directly down for reading, and with the 5050 natural white light LEDs, it is very easy on the eyes. And light can be directed up at the ceiling. Most ceilings being white, the light scatters all around the room and provides very good coverage. And with both lights on, you have the best of both worlds!
The switch is only dangling out in limbo, temporarily. I have purchased a pair of small
gray plastic boxes where the 3-way switch will be mounted. All wiring will be neatly
tucked away inside. The boxes will be strapped to the lamps, placed on either end of the
couch. This will present a much cleaner look. It will also be much more stable when
reaching for the switch if it is securly fastened to the lamp.
KITCHEN LAMP:
This "Sputnik"-like kitchen lamp hangs over the dinner table. It originally had Halogen 12-volt bulbs inside each of the colored stars. These ran on a 110-volt to 12-volt switching power supply inside the base of the lamp. It was a power hog, each bulb created a LOT of heat, and they would fail rather quickly trapped inside the star where they received no cooling. More so, the blasted switching power supply made all sorts of RFI noise on the 75-meter Amateur band. I'd have to turn this lamp off anytime I was operating on 75-meters. Well, that's not good.
The obvious solution was to remove/disconnect the switching power supply and run this lamp
on 12-volts DC. Then, to reduce the wasted energy that the Halogen bulbs created, I replaced
all of the Halogen bulbs with 12-vdc LED bulbs. Now the lamp runs cool and quiet.
I also used 3-Way light switches to control the 12-volt feed to the lamp. So there are light
switches on both ends of the Kitchen, making it easy to turn on or off from both ends of
the room. Three-Way switches wire up just like they do for 110-volt use.
I replaced the original Halogen 10 Watt bulbs with these 24-LED G4 bulbs that only draw 1.5 Watts
each. A BIG savings in power consumption (from 200 watts to only 25 watts), they don't get hot, nor
do they interfere with any of my radios. And they seem to be a whole lot brighter, too!
Available through Amazon for $13 as: Rayhoo 10pcs G4 Base 24 LED Light Bulb Lamp 1.5 Watt
AC DC 12V/10-20V Non-dimmable Equivalent to 10W T3 Halogen Track Bulb Replacement 360° Beam Angle
(White 5800-6200K)
BATHROOM LAMP:
In my bathroom there are 110-volt LED lights above the mirror. This is VERY bright for doing that closeup, carefull work on one's face. But for showers and other activities performed in the bathroom I have added a pair of 48-LED flat panels to a 110-volt fixture that is a combined light and exhaust fan. The exhaust fan is rarely ever used, but it is still functional should I ever desire to run it.
The LED panels mount on the flat metal surfaces between the 110-volt bulbs. This way they
are not blocked by the bulbs and spread a good amount of light into the bathroom. Being a rather
small room, two 48-LED panels was more than enough for such duty.
Power is brought up from the basement (Laundry room) to this "paddle" switch. It is simply
cut into the drywall and held in place with two drywall screws. That's the beauty of
low-voltage wiring, as you don't need to install an electrical box. The wires then procede
up the wall into the attic and across the rafters to the light fixture.
Here is a view with the cover plate removed. As you can see, they are extremely easy to
install since no box is required. Just cut the opening for the switch, fish your wires
inside the wall, attach to the switch, and mount the switch using two (or four) drywall
screws. Attach the cover plate and enjoy!
CONVERTING NON-12VDC DEVICES USING DC-DC BUCK-BOOST REGULATORS:
Converting NON-12vdc devices like TV's, HDMI Monitors, and other electronic devices that are DC powered but do not run directly from 12 volts DC can be easily done using a DC-DC regulator to convert the Solar power (nominal 12-14 volts DC) to the required voltage ineeded for the device. Even some 12 volt devices may not handle the voltage fluctuating (more that 6/10ths of a volt, such as with many 12-volt solid-state computers. So a more precise 12.0 volts regulator is needed.
These DC-DC Buck-Boost regulators are available from Amazon ranging anywhere from $8 up to $26 depending upon the power (Wattage) output needed.
DEVICES POWERED BY DC-DC REGULATORS
- Sony 40-inch flat-screen TV set (19 volts @ 65 Watts)
- Solid-state Mini PC (12.0 volts @ 3 Amps)
- Security Cameras & DVR (12.0 volts @ 65 Watts)
- Raspberry-Pi Linux computers (5.0 volts @ 3 Amps)
- HDMI flat-screen Monitors (19 volts @ 5 Amps)
Connectors & Power Outlets:
Being able to plug and unplug circuits and devices is necessary. Just as you can plug and unplug a livingroom lamp or table radio, so should you be able to do so with any of your 12-volt devices. A convienient and inexpensive connector is the Anderson Power Pole. This connector is easy to install, and since it is "Hermaphradidic", you use the same connector on both the Source and Load cables. There is no Male or Female connector.
Anderson Power Poles come in a handfull of connector formats, and come in any number of
sized pins that determine the current carrying capacity of the connector. The smaller "shell"
can support the 15-amp, 30-amp, or 45-amp pins.
The larger "shell" typically found on many Golf Carts and Electric Scooters, come in sizes
ranging from 50-amp, 75-amp, 120-amp, 175-amp, and 350-amp pin sizes. They also come in a
variety of colors. I use these higher current connectors for attaching batteries in the
Battery Bank. If a battery is needed elsewhere, or is failing, it can simply be unplugged and
a replacement can be plugged in in its place. That makes life simpler!
A number of Power Outlets are available as well. Anderson Power Pole connectors are available in conventional wall plate format, and as a block of 2, 4, 6, or 8 pairs of connectors mounted in a "block" that can be easily fitted onto any size plate or panel that you wish. There are also USB outlets that are driven by your 12vdc power system that provide 5-volt power to any of your USB devices. No more need for any cheap Wall-Warts taking up valuable outlet space.
Voltmeters are also available and can be placed in any room of the house so you can easily
check the status of your power system at a glance.
And there are a number of Power Pole fuse boxes that can be placed at your battery bank and
satellite units placed in various parts of the house to make wiring and protection much simpler.
"You Cannot Manage What You Cannot Measure":
Just as the title says, "You Cannot Manage What You Cannot Measure". That is to say that without some means of measuring Voltage and other data statistics such as Amperage, Time, Amp/Hours, Watt/Hours, and daily usage, you really would have NO idea if your system is healthy and working as it should. We have gauges in our cars, so should we have gauges on our power system.
A simple digital voltmeter placed somewhere where we can see it easily, can provide a wealth
of information. When it reads below 12.6 volts I know that my batteries are discharging. When it
reads at 12.6 I know that I am under load and the batteries are fine. When it reads 13.2 or above,
I know that the loads are being met and the batteries are charging. When it reads between 14.0
and 14.4 volts I know that the batteries are topped out and the Sun is blazing away.
Many Solar Charge Controllers provide LOTS of data via LCD displays, serial data ports,
ethernet ports, SmartPhone applications, and some even by way of SNMP (Simple Network Management
Protocol). Some controllers just provide the data and you have to manipulate the reports
yourself, while others put it into webpage (HTML) format.
None of my controllers provide anything more than a scrolling report on the LCD showing Battery Voltage, Output Current, Watts, Peak Power, Amp/Hours, PV Panel Voltage, and at night will scroll through the previous 7 days of stored data showing the Amp/Hours for each day. This requires me to periodically take a look at the LCD to see how well things are performing. The designer of the "Apollo" MPPT Charge Controller is working on a new version that will support a data port that can be connected to a computer to perform the data collection and display function.
The "Morningstar TS-MPPT-45 TriStar 45 Amp Charge Controller 12-48V" supports SNMP over an ethernet port. It also has a built-in webserver that provides a nicely organized display of performance data. This beauty sells for a mear $478 !!! Yeah, that's way outside my budget right now. Maybe some day.
Pumping Water with 12-VDC :
Pumping water with 12-volts D.C. is just as easy as pumping water from a well or water
tank using 110 volts A.C. The main difference is that there are indeed fewer water
pumps available on the market that deliver the pressure (PSI) and flow rate (Gallons per Minute)
that would approximate the water pressure and flow we are accustomed to from a city provided
water source.
But the fine folks at Backwoods Solar (see URL in the Resources section, below)
have a Pressure or Boost pump that meets those specs for an affordable price. The
Aquatec 550 runs on 12-volts D.C., delivers 3.5 GPM at 60 PSI. This is ideal for
pumping water from a cistern or storage tank into an Expansion tank, then into the home.
These pumps are used a lot in RV and travel trailers. But be prepared - they require
nearly 17 AMPS in order to deliver that much pressure at that flow rate. So I recommend
placing a 55 Amp/Hour battery near the pump so that your Solar system can charge the
battery across a lower gauge cable, then when the pump needs high current, it can draw it
from the local battery. Since the pump *should* only be used for a few minutes at a time
this allows plenty of time for the local battery to be recharged.
The Aquatec 550 contains a pressure switch that turns ON at around 45 psi then turns OFF
when the pressure reaches 60 psi. This allows your Expansion tank to provide the bulk of
the water demand in the house, and the water pump then only needs to turn on to replenish
the Expansion tank. It *can* provide steady flow for 10 or 15 minutes at a time when the
Expansion tank has run out of pressure and you still demand water flow. But this pump
is NOT intended for continuous duty, but can easily keep up with my 2-person home and our
water demands.
Aquatec 550 12-volt 60psi 3.5 gpm Pressure Pump
Here is a look at my Aquatec 550 pump that pumps water from the 170-gallon cistern,
through these 3 filters and into the house. To the left of it is a smaller pump that
pumps water from the Rain Catchment barrels and feeds the outdoor water faucets. That
is used primarily for watering the garden.
There is a 55-Amp/Hour battery located in the Well Room near these pumps. This way
the battery can be recharged at a few amps over a long cable run from the main Solar
battery bank, while being able to buffer the brief high current loads needed to run the
pumps. The pumps spend most of their time off, and then turn on for only a couple minutes
to re-pressurize their respective Expansion tanks (20-gallon on the house system, and 2-gallon on
the outdoor water faucets).
Basement Stairwell Night Light :
A simple 12 LED panel mounted on a plastic electrical box serves nicely as a night light
near the bottom of my basement stairwell. This lights up all of the steps and a goodly portion
of the basement, too! It consumes roughly 2 Watts, compared to most incandescent screw-in
bulbs that consume 4 to 7 watts.
Future Projects:
USB outlets for cellphone, tablets, and other devices
Ceiling fans (lightingdirect.com)
12-volt pumps for Rain Water Catchment system to water lawns and gardens
Yard Accent Lighting - change incandescent bulbs to LED and run on 12-vdc (use an Arduino/PIC/R-Pi as timer)
Using a DC-DC Converter to power Laptops, TV's, and Diskless Workstations:
Our households are full of devices that operate on oddball voltages and require special Wall-Warts that plug into the wall or a Brick that is inline with the power cord. Many laptops run on 19 vdc at a couple amps, flat-panel TV's sometimes have the power supply built in, but more and more I see them with a Brick inline with the power cord. My TV runs on 19 vdc and consumes only a maximum of 60 watts. I also have a few Diskless Workstations that require exactly 12.0 volts (plus or minus 0.6 volts) to operate. With appliances like these, a DC-DC converter makes converting them to run on the 11 to 14 VDC from our Solar Power System quite simple. Just set the trim pot to the desired outputr voltage and you are good to go!
The in-line Brick actually contains an AC to DC rectifier followed by a DC-to-DC converter.
So we are just skipping the rectifier portion since our source is already direct current.
Available on Amazon for $13 is the "Gowoops 2PCS 150W DC-DC 10-32V to 12-35V Step Up Boost Converter Module Adjustable Power Voltage"
Using an APC SmartUPS 3000 UPS as a Whole-House Inverter:
Though most things in the household can be run on, or replaced with, things that run on 12 vdc with little effort, there are some items that are simply easier to run off of an Inverter. Basically, an Inverter takes the DC from batteries as an input, chops it into pulses, passes that through a transformer to step it up from 12 or 24 or 48 volts to 120 volts, and feeds that to the 120vac loads. A good inverter will use stair-step technology (rather than pulses) to ramp the DC voltage up and down to approximate a sinusoidal waveform so that it looks like a normal AC waveform. This is MUCH cleaner and produces FAR less noise. Besides, AC devices are meant to work with such a waveform.
I have two APC SmartUPS 3000 rack mount UPS's, the latest purchased for only $25. They are good for 3000 VA (Volt/Amps) which is approximately 2500 Watts. These things are BEASTS, measuring in at 19" W x 5-1/4" H x 25" D and weighing a TON when fully loaded with 8 NP12-7 SLA batteries. The batteries are wired to make up a serial/parallel string totalling 48 volts. APC states that these UPS's can run 24 hours per day at 110% rated capacity, are stair-steped to produce a sinusoidal waveform, and are more than 95% efficient.
I don't plan to push them anywhere near that hard. My plan is to attach a string of eight 6-volt deep-cycle Golf Cart batteries (210 AH) externally, that will be charged not by the UPS - since the UPS will never have AC input applied to it, but will be charged by a Solar Charge Controller attached to its own set of PV panels.
That is the plan, anyway. We will update this section of the website as the project progresses...
Convert a Feit 4-foot LED Shop Light to 12vdc:
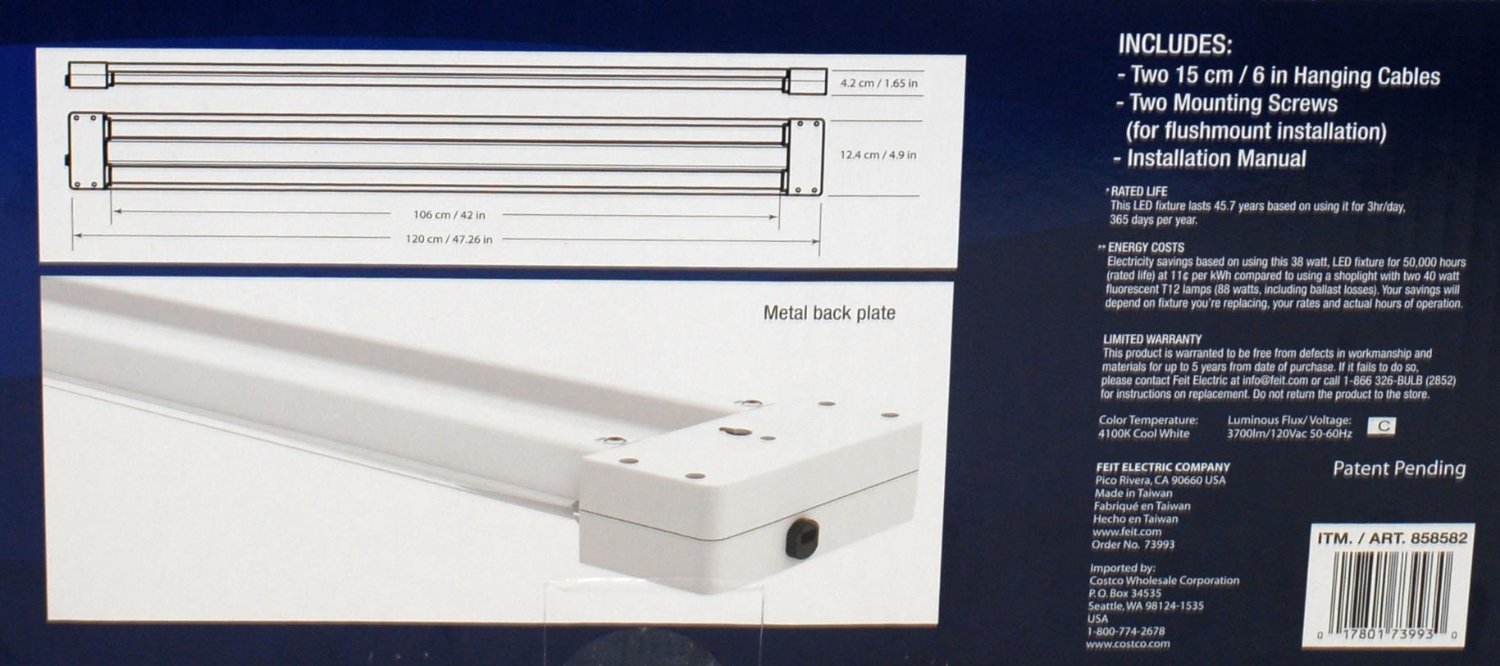
4100K Cool White
3700 Lumens
38 Watt (using the 110vac switcher)
50,000 hours expected lifetime
I have several of these fixtures and really like them. VERY white light, very bright, and
most of all have the potential to be converted to 12vdc use only. This project is on my TODO
list, and will further my endeavor to convert yet more of our household to 12VDC only.
12VDC Replacement Hot Water Heater Elements:
...ranging from 75 watts to in excess of 300 Watts (25 Amp)...
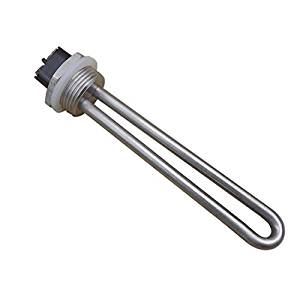
Resources:
- Handy Techniques for fishing wires through walls and ceilings
- 12VDC Power Yahoo Group
- DIY Solar for U - Apollo Solar Charge Controller
- Uni Solar (went bankrupt)
- Solar Ypsi - an entire community promoting Solar energy on homes and businesses
- Ann Arbor Solar Club on Facebook
- DTE Energy Green-Power - Buy units of Green Energy each month. Choose how much your avergae KWH usage is, and what percentage of your bill you would like to offset with Green energy sources.
- The Hybrid Electric Home - Individual Rural/Farm electric power plants using 36-volt products, a multi-million dollar industry killed off by the Rural Electrification Act
- History of the Delco-Light home power generators
- History of American Wind Chargers
- USA Light / Direct Lighting
- Northern Arizona Wind & Sun
- Backwoods Solar - The BEST darn catalog of Solar/Hydro/Wind products and helpful information on how to install and use it, too!
- Microchip AN1521 Application Note for MPPT Charge Controllers
Thank You for Your Interest in Solar and 12 VDC !!!
Jay Nugent - WB8TKL
1316 Oak Street
Ypsilanti, Michigan 48198
jjn@nuge.com
(734)484-5105 /home & office
(734)649-0850 /cell
1316 Oak Street
Ypsilanti, Michigan 48198
jjn@nuge.com
(734)484-5105 /home & office
(734)649-0850 /cell
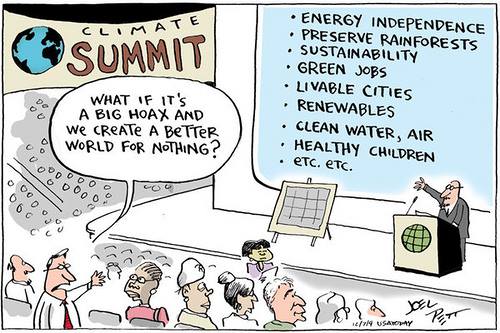
--- the end ---